White Paper
Finding Balance: Why Data Centers Are Moving Toward Custom Mechanical Solutions
Custom mechanical solutions are defining tomorrow's data center
What's Covered
- New Challenges, New Choices
- Finding Balance
- Innovation Through Design
- Customization at Scale
- A Shift in Mentality
For years, data centers have relied on off-the-shelf mechanical solutions to keep costs low and scalability options obtainable. Standardized hardware is no longer suited to the specific demands new data centers now face.
Innovation is a must.
As 5G begins to roll out across the U.S., it will bring a massive increase in data production, data storage needs, and energy demands. Carbon-neutral goals will push data centers to explore new solar, hydro, wind, and geothermal technologies.
And while hyperscalers with large nodes in Chicago, the upper Northeast, Phoenix, and the Carolinas look for the right mix of custom and stock hardware to handle these anticipated increases, they’re also placing a renewed focus on secondary markets like Minneapolis, Reno, and Denver. Fiber optic expansion will be the backbone of these new data centers, where edge computing brings its own unique factors and field requirements.
Customization at Scale Required More Focus on Design, Engineering, and Innovation with Less Attention to Standardization
Data centers, both large and small, must begin to adapt their facilities and technology to keep up with these dynamic needs.
Although there’s no perfect formula for adaptation, custom mechanical solutions that are collaboratively engineered, manufactured, and assembled provide the flexibility and scalability needed to adapt and grow.

New Challenges, New Choices
It’s estimated that 1.7 MB of data was created every second by every person on the planet in 2020 (approximately 1 gigabyte every 10 minutes).
Experts say those numbers will continue to grow, predicting humans willgenerate 463 exabytes of data each day by 2025.
To put that in perspective: if one gigabyte is represented by the size of the Earth, an exabyte is the size of the sun (see figure 1).
Now, imagine 463 suns worth of data being created each day.
How do data centers plan for this amount of growth?
Aside from expanding existing hyperscale data centers, new data districts are being built in secondary markets while fiber networks are continuing to be built out. The ability to generate on-site renewable power is also becoming a necessity.
Companies are recognizing their global responsibility in (and reaping financial incentives for) adopting renewable energy sources for on-site power generation. As reliance on 5G and IoT increases, storage will be crucial to long term success. Additionally, the amount of data being stored is expected to grow to 8.9 zettabytes by 2024.
Interestingly, energy use in global data centers has plateaued in recent years with just 205 terawatt-hours (TWh) being the average in 2018 (approximately 1% of global electricity use). While a number of factors are at play, structural shifts in the industry are key. Fiber and renewable energy companies will need to keep up with data center infrastructure through innovation - relying on custom mechanical solutions for their installations as well.
Finding Balance
Data center infrastructure is changing dramatically among hyperscale players and the market is determining how they pursue those changes.
Compute platforms that are 100% custom will need more standardization. Others that have been designed with fully standardized mechanical solutions will need to move toward customization.
Right now, neither approach is perfect. But data centers are looking for that perfect balance. And more importantly, they’re designing solutions to get the mix right.
Companies are also looking for ways to shrink current computing power into much smaller nodes that can be placed closer to sources where data is being created to reduce latency issues. Because electric vehicles and IoT devices need to disseminate so much information from the edge to data centers, custom enclosures will be required.
Many data centers — especially in secondary markets — have started creating an on-prem/off-prem public-private cloud combination that places customized racks in an office building with connectivity back to their cloud. Seen as a new version of edge cloud, it’s a method that’s growing in popularity and driving the adoption of customized solutions.
In short, customization at scale will be the new standard.
Innovation Through Design
When an engineering team wants a customized mechanical solution, they traditionally begin by calling their existing vendors. Most vendors, however, don’t design and manufacture custom mechanical solutions; they adapt existing, standardized ones.
At best, the engineering team receives a partially customized solution and settles for something that minimally addresses their needs.
Inversely, the companies that are building the flexible and adaptable data centers of the future have realized customized mechanical solutions must be designed and manufactured from scratch. It’s the only way to meet the unique requirements each environment and market requires.
There’s no room for fast followers when it comes to customized mechanical solutions for data centers and edge computing.
Custom enclosures of any size begin with an engineering team, a blank sheet of paper, and manufacturers with the DFM and DFX design services to build speed, flexibility, and scale into every decision.
The companies that are going to do well are the ones that put a lot of emphasis on design, engineering, and innovation. They're not interested in buying a white box from an OEM because they take pride in their ability to innovate through design.
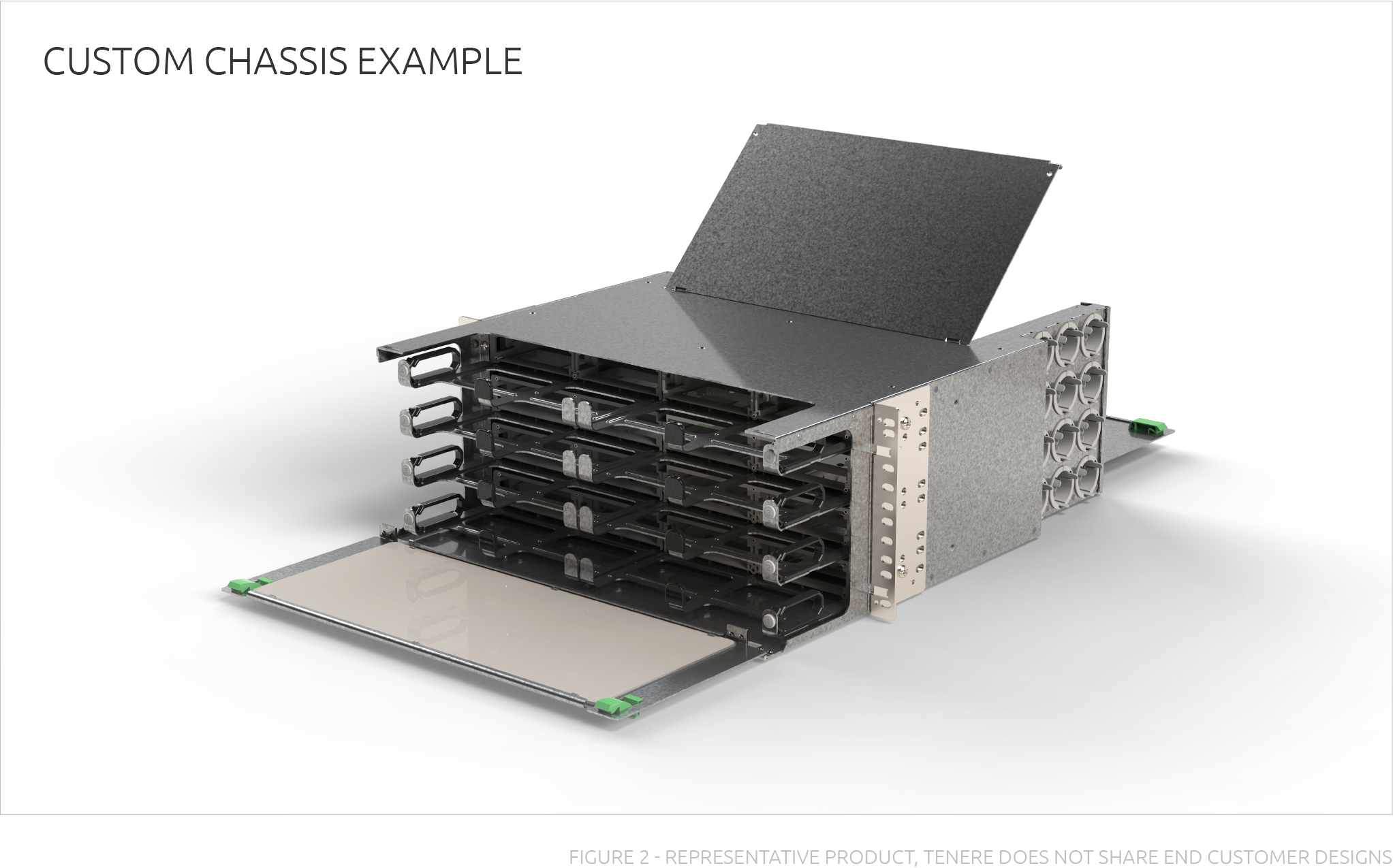
Whether they’re trying to increase density or keep field compute physically dry, companies need an optimal solution, not a “close enough” one.
Thanks to custom mechanical solutions that are designed from the ground up, data centers are getting exactly what they need. And the solution is an exact match to their goals, as opposed to having extra space in a standard box that gets left half-empty.
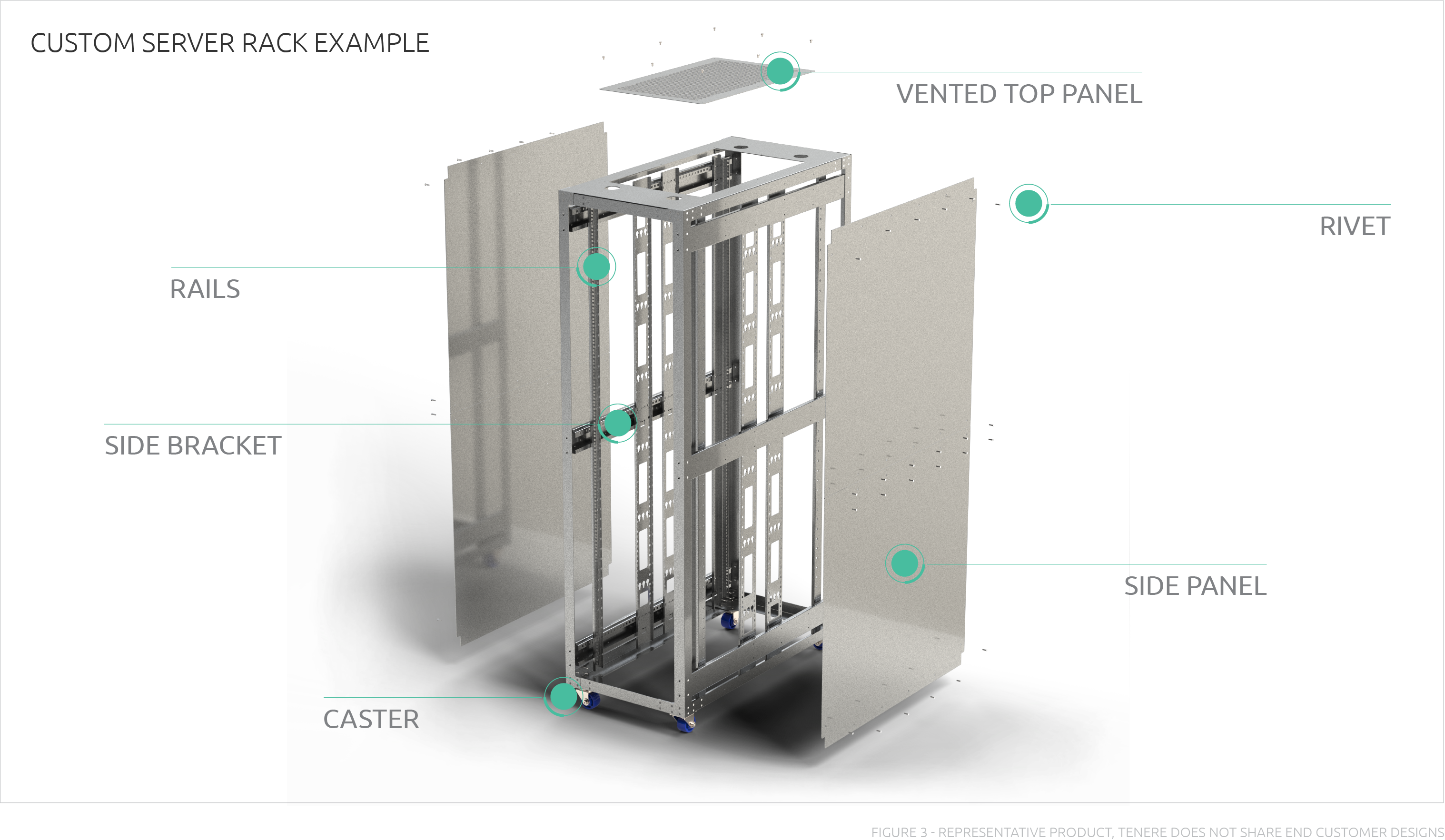
Customization at Scale
The traditional trade-offs companies once thought about customization— direct costs, total cost of ownership, and inability to scale — no longer exist. Today, customization at scale achieves the same efficiencies as stock.
One of the main reasons data center companies have gone with off-the-shelf solutions is because parts exist in a warehouse somewhere; they’re easy to get. If you wanted ten, no problem. But doing that at scale quickly became an issue. One hundred? Wait a month. One thousand? Wait a quarter.
This is a huge issue for the hyperscalers of today who are looking for customized solutions for massive deployments.
Fortunately, modern manufacturing technologies and engineering capabilities have eliminated those hurdles.
Because typical deployments are so large now, scalability is a moot point. And whether a deployment is tied to 5G, fiber, or an entire data center, direct cost is no longer an issue either. Even the total cost of ownership comes down when compared to the inefficiencies of a “close enough” stock solution.
Factory capacity and soft tool fabrication in North America — coupled with engineering knowledge and expertise — have created major shifts in the way customization is now achieved at scale. Today’s manufacturers can produce thousands of customized parts within weeks.
Tennis shoes are a good example of customization at scale. A few years ago, a custom pair of shoes were not an option for most consumers; the costs were too high. Even those who could afford them weren’t willing to wait; it took too long. Today, however, custom tennis shoes can be designed online, ordered, paid for, and shipped within 48 hours.
The same thing has happened in large-scale manufacturing, especially among hyperscale data center players.
Artificial intelligence, machine learning, better software, and flexible manufacturing automation and robotics have also helped bridge the gap between scale and cost.
Customization in Action
A large hyperscaler settled on using a standard rack, but once they put it into production they soon realized that having a custom bracket leveler would make the rack more efficient in their data center. Working with their current rack supplier wasn’t a great option. Custom parts were not their expertise and could take several months or longer just for a prototype. So they approached a custom manufacturer (Cadrex) for an engineered solution.
Within two weeks, Cadrex engineered the prototype, painted it, and hand-delivered it. It worked so well they are considering other ways customization can improve data center installation and performance.
That’s how the power of speed, innovation, and customization win the game. That’s customization at scale.
A Shift in Mentality
It’s clear that a fully standardized or fully customized solution is not the answer to the demands and challenges data center companies face.
But customization has a strong future and it will continue to evolve.
As such, hyperscale players are recalibrating their approaches to customization and standardization. Moving from sku-based, off-the-shelf solutions to unique products designed for specific features — and putting more focus on innovation — requires a shift in mentality.
If you're considering customization to optimize the performance of your technology in or outside of the data center, you need partners that have customized mechanicals in their DNA.
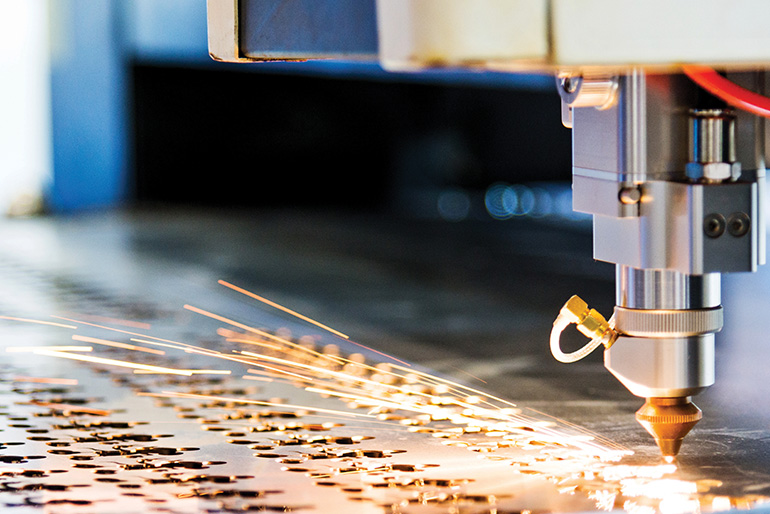
About Cadrex
Cadrex is one of the largest manufacturing partners in North America, with 20 facilities located in nine states and Mexico. As a leading custom mechanical solutions provider for the most innovative companies in the world today, we offer a unique breadth of capabilities and technical expertise that allow us to rapidly bring customer programs from concept to scale. In addition, our decades of specialized experience designing and manufacturing for information communication technology, warehouse automation & robotics, kiosk & gaming, aerospace & defense, renewable energy & electrical infrastructure, and medical sectors make us a trusted partner in our customer's supply chain.