Precision Machining
home / capabilities / precision machining
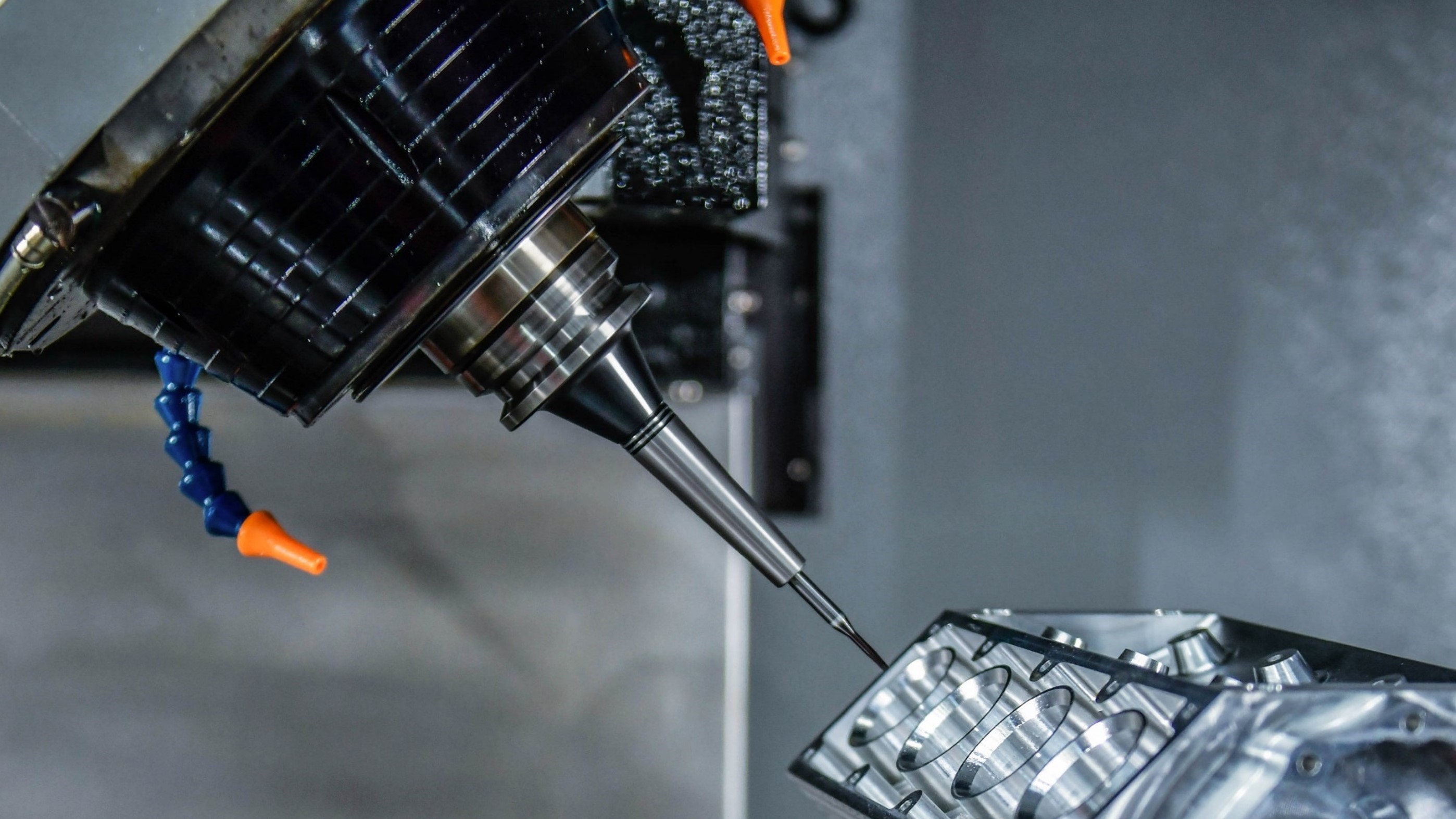
Precision Every Time
Our commitment to success for our customers goes beyond hard work and dedication — it means precision every time. As one of North America’s leading precision machining companies, Cadrex has invested in some of the industry’s most powerful automation for precision CNC machining.
From integrated robotic cells to 100-plus vertical, horizontal, and 5-axis machining solutions, our climate-controlled, 24/7 lights-out capabilities can accommodate project runs of all sizes. Our experience manufacturing complex precision-machined parts and our substantial investment in state-of-the-art machinery make us the perfect partner for your next program. With our complete breadth of capabilities, we can scale your programs as they grow.
Precision Machining Capabilities
- 250+ Plastic & Metal CNC Machining Centers
CNC machining allows manufacturers to create plastic or metal products with repeated results quickly and accurately. We have more than 250 plastic and metal CNC machining centers strategically located at our sites across North America. Our designers and engineers work together and with our clients to determine the best manufacturing methods and materials for each project. CNC machining can be preferable when working with plastics because it is more precise than injection molding and is more compatible with a wide range of materials. There are a handful of commonly used metals in CNC machining. Manufacturers consider how the part or item they are creating will be used, temperature requirements, and weight and size to determine the base material for individual projects.
- Robotic and Manually Fed Vertical, Horizontal, and 5-Axis Machining
CNC machines remove material from a workpiece to shape it into a final design. With CNC milling, a block of material remains stationary while tools shape or cut the workpiece. Horizontal milling machines have a spindle that is mounted horizontally. Vertical machining centers can be used for drilling and plunging cuts. A 5-axis CNC machine can move tools or workpieces in at least five directions, and it can work on five sides of a workpiece at one time.
- Automated CNC Milling
Milling centers have moving tools that remove material from a fixed workpiece. They are often equipped with an automatic tool changer (ATC), a system that automatically changes the tools in a CNC machine without the need for human interaction. They all have a stationary workspace that secures the workpiece to minimize its movement. With milling machines, removed material automatically falls off the workpiece without interfering with the tool.
- Bar-fed or Manually Loaded CNC Turning with Live Tooling
Milling and turning are different in that with a milling center, tools move around a stationary workpiece, whereas with turning centers (or CNC lathes), the machine tools remain stationary as they cut a rotating workpiece. Turning starts with a rotating bar of raw material, which can be fed into the machine manually or with an automatic bar feeder. Live tooling is when a custom tool, powered independently by small motor, is attached to the stationery lathe, essentially turning it into a milling center as well.
- Waterjet Cutting with 5x10ft Bed
A waterjet cutter uses a high-pressure stream of water like a laser beam. It has the ability to cut a wide range of materials, particularly those sensitive to high temperatures. Sometimes in waterjet cutting, the water is mixed with an abrasive substance to cut hard materials.
- Bar-fed Swiss Turning for Precision Machining Hundreds to Thousands of Parts
Swiss turning, also known as Swiss machining, is a CNC machining process used to produce small parts and parts with complexity. Most CNC Swiss lathes use main and secondary spindles (which perform additional or secondary operations), and they often incorporate live tooling. Swiss machining is often used when projects require small, complex parts to be produced in mass quantities.
- Polishing, Blasting with Multiple Media & Passivation Finishing
Our capabilities at Cadrex go beyond the initial design and mechanical assembly. We operate various finishing processes to ensure products look and feel as well as they perform. Media finishing removes rough edges or small pieces of extra material, while passivation finishing adds a layer, coat, or shield on material to protect it from the environment.
- Grinding
CNC grinding involves removing material from a workpiece using a rough, rotating abrasive wheel.
- Laser Etching
CNC laser cutters use a laser beam to etch, mark, cut, or weld a source material.
- Wire-Fed Electrical Discharge Machining (EDM)
Electric Discharge Machining (EDM) uses sparks or electrical discharge remove material from a workpiece.
- Aluminum, Steel, & Magnesium Casting
Metal casting is a process in which molten metal is poured into a mold where it cools and hardens into a desired shape. Precision sand casting is a manufacturing process in which molten metal is poured into a mold packed with sand in a specific shape or pattern. Learn more about sheet metal fabrication and stamping at Cadrex.
A Critical Component
Machining Automation
Cadrex continues to invest in high-quality, state-of-the-art precision machining equipment, automation, and robotics. We research and incorporate the latest trends and technology in automation as we strive to continuously offer top efficiencies, quality, and ergonomics. Depending on your program size and requirements, our automation engineers will determine if robotic operators will benefit your program. Learn more about BI, automation, and robotics at Cadrex.
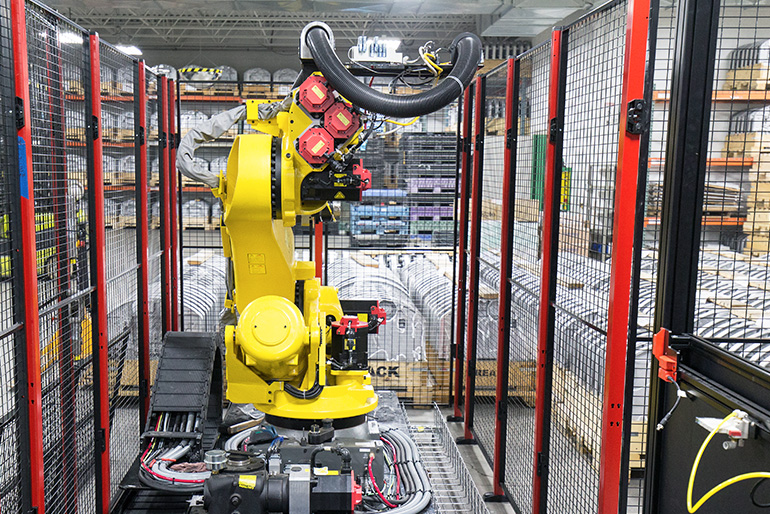
How it Works
Precision machining is a manufacturing process in which a raw piece of material is turned into a desired shape. A computer numerical control (CNC) machine is an automated machine often used in the precision manufacturing process. CNC machines perform tasks programmed by digital software. knowledgeable workers can operate a fleet of machines by utilizing computer software. Computer-aided design, or CAD, software is used to build a model of a design. Operators upload design specifications from the software to instruct the machine on how to process materials. Learn more about engineering and prototyping at Cadrex.
The two most common methods of CNC precision machining are milling and turning. Turning involves a rotating bar of raw material, or workpiece, and stationary cutting tools remove material to create the desired part shape, which is programmatically generated through computer-defined cut paths. Milling differs from turning in that the workpiece remains stationary while specialized rotary cutting tools remove material to turn the piece into a desired shape.
Many other specialty machining processes exist to supplement traditional machining. These processes are typically used in specific applications, and our engineering experts creatively determine the best practices needed during the beginning stages of onboarding a new program.
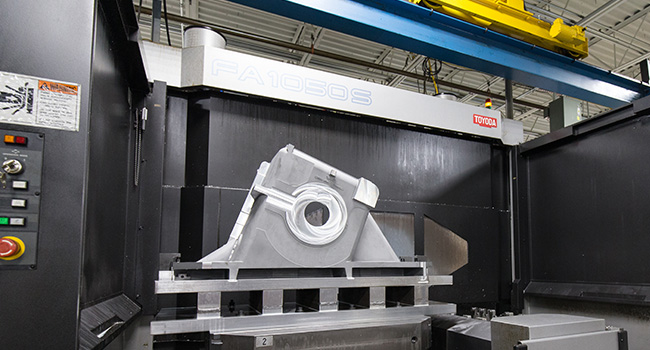
Uses of Precision Machining
Precision machines and manufacturing provide precise parts and products in mass quantities to many industries. Mass-produced products that need to be highly accurate benefit from precision machine production. You will find evidence of precision machining in parts used for military equipment and planes in the aerospace and defense industry, in electrical components in the renewable energy and electrical infrastructure industry, and in surgical devices in the medical industry. Every industry across the board relies on precision machining.
Common Machining Materials
Aluminum (Including Medical)
Aluminum 6061, Aluminum 7075
Copper Alloy
Copper C110, Brass
Steel (Including Stainless)
300 Series, Inconel, 17-4, 13-8, 15-5
Other
Plastics, Magnesium, Titanium
Related Links
White Paper
CNC Machining Starter Guide
Read our introduction to basic CNC machining terms and definitions, including an in-depth look at precision CNC machining. We’ve come a long way since shaping metal with a hammer...
White Paper
Building The 21st Century Critical Infrastructure: A Roadmap To A More Connected Future
Society is amidst a massive shift in how technology and daily lives interface. The internet, interconnectedness, and information technology are no longer just novelties; they are necessities that fuel the foundations of even our most basic needs. ...
White Paper
Disrupting Energy: How Long-Term Energy Storage is Changing the Way We Power Our Lives
Today, the United States gets around 80 percent of its energy from fossil fuels like coal, natural gas, and crude oil...