Blog
Why Automation Is The Future Of Custom Plastic Injection Molding
Custom plastic injection molding is a demanding industry, making automation key to producing the highest-quality parts at the best price possible. Here are some reasons why, along with a few tips on what to look for in a provider.
January 13, 2022
It’s a well-known fact that manufacturers who wish to offer competitive pricing and the best part quality must automate their production processes whenever possible. This is just as true for sheet metal fabricators and those doing mechanical assembly as it is for stamping houses and plastic injection molders.
In a typical custom plastic injection molding manufacturer operation, parts must be extracted from reaching deep inside molding machines. Secondary operations such as trimming and hole drilling are often required, and for parts where insert molding is called for, machines may have to stop long enough to perform this task as well. It’s not only tedious and tiring work but can also have implications for cost and quality. Automated systems can eliminate human fatigue, reduce cycle times, and mitigate the risk of injury, making them a necessity in any manufacturing process.
Problems Automation Can Solve
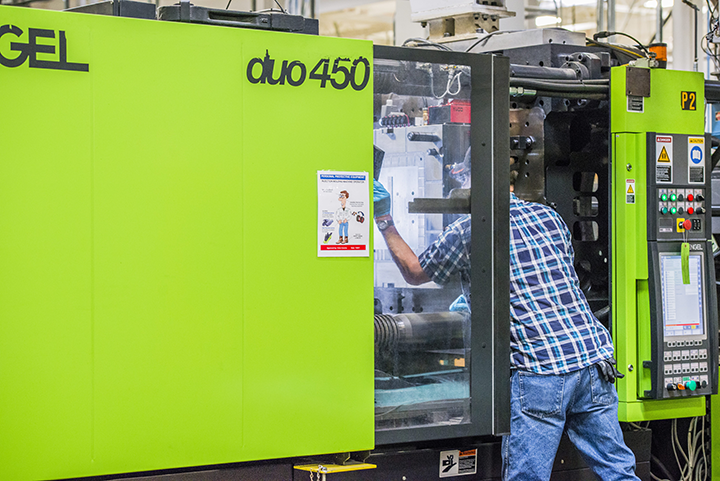
Much of the labor in a plastic injection molding plant is demanding work but is increasingly necessary for manufacturers to meet the needs of their customers. Here's an all-too-common example: a custom injection molding firm supplying small parts for a fiber optics enclosure. The company has three machines, each equipped with a single-cavity mold, and because the process is not automated, there's an operator standing in front of each one. But since human operators are subject to physical limitations, repetitive and ergonomically taxing tasks can make the process less than predictable. Even brief stoppages can cause the mold cavity to cool down slightly, leading to small quality deviations. And as any production floor supervisor can attest, the machine’s OEE (overall equipment effectiveness) level could be higher—often much higher.
By automating, this same supplier could eliminate many of their cycle time variations. Mold cavity temperatures are now more consistent, so part quality levels increase. Load and unload times are also much faster, especially for those parts that require an insert or overmolding. And because robotic machine operators can reach much farther and more quickly without strain, multi-cavity molds are far more feasible. In this example, the manufacturer doubled the number of mold cavities and used just one operator for the three machines, assigning the other two to more important tasks. Everyone wins.
Find a Manufacturer Who Can do Both (Industry Expertise and Automation)
Successful implementation of a custom plastic injection molding automation strategy is not for the faint of heart. Plastic injection molding and automation technology are both complex, deeply technical subjects. A wealth of injection molding design knowledge is necessary in order to produce accurate parts efficiently and cost-effectively. Molding engineers must have an understanding of DFM (design for manufacturing) principles, polymers and fill materials, design considerations for overmolding, insert molding, and multi-cavity tools, as well as access to advanced CAD/CAM software and mold flow analysis tools.
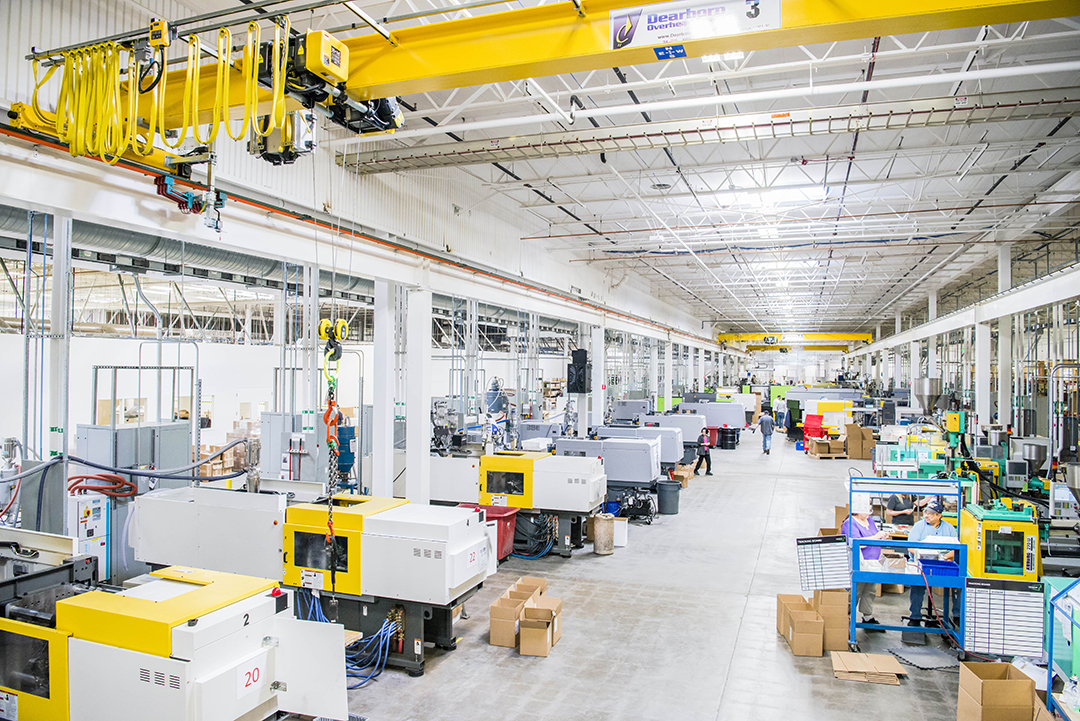
Automated injection molding raises this bar even higher. The manufacturer must not only be an expert in molding and manufacturing practices but also understand how to use and program industrial robots. This can include complications like how to deal with side entry loading, pick and place robotic automation, or how to integrate vision systems into the production process to speed throughput while ensuring part quality.
The Fringe Benefits of Automation
It's also important to note that the benefits of automation go beyond the direct production efficiencies offered by industrial robots. Manufacturers who automate their production floors have more time to streamline their other processes. For instance, they can gather and analyze production information and use it for continuous improvement projects. And because there are fewer inefficiencies in automated manufacturing facilities, lead times are generally shorter with fewer surprises. It seems that industrial automation is the answer to much more than labor shortages; it allows North American-based manufacturers to offer competitive costs, increased efficiency, and superior quality in their plastic injection molded parts. It's the clear path forward for manufacturers of all kinds.
Recent Insights
News
Blog
White Papers