Blog
Should Your Sheet Metal Manufacturing Partner Be Tech-Savvy?
June 4, 2021
There’s no shortage of reasons for manufacturers to embrace automated sheet metal production and other forms of advanced manufacturing technology. For starters, it offers better lead times, tool life, and part quality. There’s increased overall equipment effectiveness (OEE), leading to more cost-effective production and higher throughput. And opportunities for continuous improvement abound. The list goes on.
Still, why should you as a procurement person or product designer care how your partner produces sheet metal parts, as long as you’re getting a competitive price, the finished products meet specifications, and they arrive at your receiving dock on time? It’s a fair question, but sorry to say, it’s also a bit shortsighted.
Taking Sheet Metal Manufacturing Digital
Suppliers that dance on the cutting edge of technology are quite simply more efficient. They make far fewer mistakes than their less advanced competitors, which translates into no surprises, no unpleasant phone calls to say the parts will be late. Just as importantly, these suppliers are better equipped to provide the decades-old manufacturing trifecta just described, as well as a few benefits you might not have expected. More on this later.
But what does “advanced technology” really mean? And what’s up with the current buzzwords, Industry 4.0 and its little brother, the Industrial Internet of Things (IIoT)? The first of these refers to the increasing digitalization of design and manufacturing processes currently underway, offering capabilities such as virtualization and machine learning to manufacturers of all stripes and sizes.
The second refers to sensor-based data collection and software-powered analytics. When properly implemented, this powerful combination gives sheet metal fabricators and other manufacturers significant insights into their shop floors. The result? Smart factories able to produce more parts in less time, with much less waste and human intervention. And because the managers responsible for these factories have more timely and accurate information at their fingertips, they can make smarter business decisions, working proactively rather than reactively as in traditional manufacturing facilities.
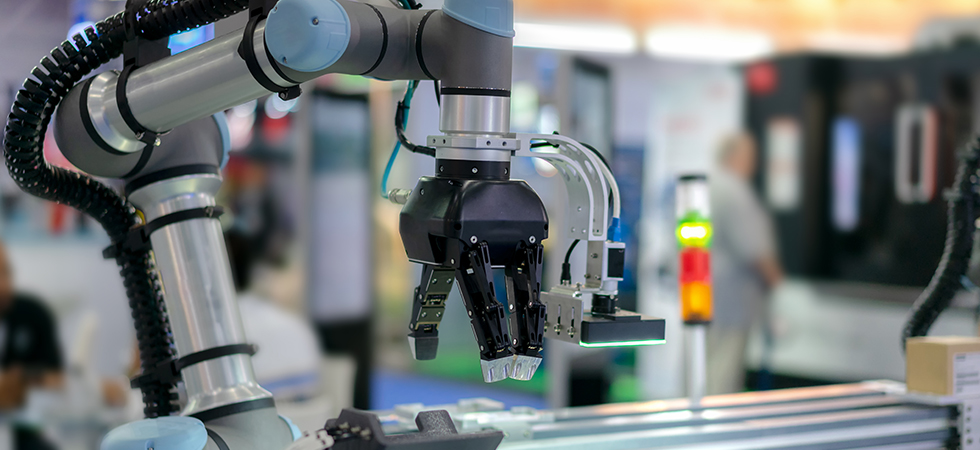
Loving R2D2
Of course, smart factories also require automation. In some cases, lots of automation. That generally means robotic machine tending and automated material handling, welding, and paint or powder coat lines, but it also requires remote monitoring systems that communicate with mobile devices, alerting their human counterparts when things go awry. The end goal of all this is lightly attended or even unattended manufacturing, leading to lower production costs that ultimately benefit the customer.
This "lights out" manufacturing is the Holy Grail of fabricating and CNC machine shops everywhere. Unfortunately, very few have achieved it, at least not yet. For starters, it takes significant investment, not to mention "the right stuff" in terms of knowledgeable personnel and controlled, highly predictable sheet metal fabrication processes.
That said, success here depends on the right mix of part geometry and materials, with higher quantity, simpler parts at the head of the lights-out pack. As you’ll see, however, there’s plenty more to this equation, and even complex, low-volume production can be realized in an automated fashion.
And to those naysayers who complain that robots are killing off all the good-paying jobs, nothing could be further from the truth. As a recent article in The Fabricator suggests, automated sheet metal operations are generally more successful than those that avoid robotics, leading to increased company growth, and ultimately, more jobs. Again, which would you prefer as a supplier?
Turning Out The Lights
So what are some of the technologies needed to master automated sheet metal fabrication? Consider a manufacturer that produces a wide variety of chassis and boxes for their clients in the network infrastructure, fiber optic, and renewable energy industries. These custom sheet metal enclosures are constructed of individual pieces of sheet metal that have been cut to the desired shape, bent on a press brake, then riveted, spot welded, or otherwise joined into the finished product.
It sounds simple, but the process is anything but. In this scenario, a computer-controlled material handling system feeds metal sheets from a storage tower to a laser cutter, or perhaps a punch-laser combo machine. For larger parts, a robot will then transfer the cut blanks via a conveyor system to a machine known as a panel bender, while smaller ones are routed to robotically-tended press brakes, which can load and unload the machine with little to no human interaction.
Each of these machine tools takes instructions from CAD/CAM or special nesting software that is more than likely integrated with the company's ERP and MES (manufacturing execution) systems. They’re also capable of automatic tool changes, and in the case of the press brake, can even perform their own setups. This makes even low-volume production and prototype development both fast and cost-effective.
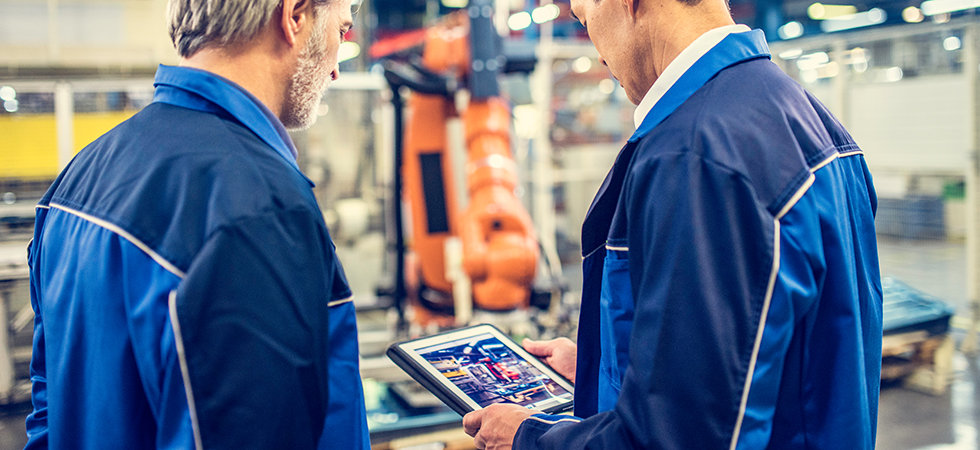
Beyond The Factory Floor
It’s cool stuff, to be sure, but it doesn’t stop there. Because the different software systems speak to one another, the shop and its employees have access to a single source of the truth. There are none of the islands of information and lack of transparency so prevalent in less integrated manufacturing companies. Best of all, real-time tracking and alerts keep everyone informed of each job’s production status throughout the manufacturing process, eliminating potential problems before they can rear their costly, disruptive heads.
Despite all this high-tech wizardry, no sheet metal fabricator can operate long without a skilled team of fabricators, machine operators, and manufacturing engineers at the helm. These people help to ensure that the train stays on the tracks. They assist with setups and tooling preparation. They perform planning functions and troubleshoot processes. And when appropriate, they work with customers to make parts more manufacturable via established DFM (design for manufacturability) practices.
To those purchasing precision sheet metal parts and assemblies, this last function is invaluable. Through collaboration with their customers and internal teams, manufacturing engineers play a critical role in keeping costs down. For example, continuous analysis of production data helps determine where process improvements can be made, while knowledgeable decisions over whether to use soft vs. hard tooling serve to reduce up-front investment. Lastly, manufacturing engineers assure that customer projects move seamlessly from the concept and prototype stages to final testing and full-blown production.
Put it all together and you'll realize that partnering with a smart manufacturer gets products to market more quickly. Costs are reduced, unpleasant surprises eliminated. So if you want to hear more examples of how a top-notch, highly automated, and tech-savvy sheet metal fabrication partner can help your business, or just want to chat about smart manufacturing in general, feel free to give us a call. We’d love to discuss it further.
Recent Insights
News
Blog
White Papers