Blog
Semiconductor Equipment Manufacturing: Optimizing Supply Chains in North America
The semiconductor manufacturing industry is undergoing rapid transformation driven by technological advancements, increased demand for AI and electric vehicle (EV) chips, and geopolitical shifts.
March 26, 2025
The semiconductor manufacturing industry is undergoing rapid transformation driven by technological advancements, increased demand for AI and electric vehicle (EV) chips, and geopolitical shifts. Needless to say, the semiconductor industry and the companies that fabricate the equipment used in the industry have had to take on a new challenge of high mix manufacturing.
What Exactly is a Semiconductor?
A semiconductor is a material between a conductor and an insulator, which creates the ability to conduct electrical current. There are many things that can be changed based on what the application requires, including electrical resistance, conductivity (which can be changed by the temperature), or number of cores (based on how it processes information).
Semiconductors are not a new thing, in fact, the first semiconductor goes back over a century. Each application requires a different type of semiconductor, they are not made equally. Modern semiconductors are used in a variety of electronic products from radios to computers and smartphones, electric vehicles, and AI computers.
The Future of Semiconductor Manufacturing
Market research suggests that the global semiconductor industry is projected to surpass $1 trillion in revenue by 2030 (McKinsey).While demand for smartphone and personal computer chips has declined slightly in recent years, the need for AI chips and automotive semiconductors has surged.
Semiconductor OEMs need strong manufacturing partners to keep pace with industry changes. The complexity of semiconductor equipment and the manufacturing of custom parts requires many different processes including precision machining, sheet metal fabrication, plastic injection molding, casting, specialty finishes, and rigorous testing. The high-mix nature of semiconductor manufacturing today means that finding partners with the right expertise and close working relationships is critical to success.
Identify Experts in Advanced Manufacturing Capabilities for Semiconductor Equipment
Precision is the most important element of manufacturing semiconductor equipment. There are several types of equipment that go into a semiconductor manufacturing environment, which all require precise attention to detail and specific manufacturing criteria.
Vacuum Chambers:
Producing sensitive electronic devices requires a controlled environment. Vacuum chamber manufacturing provides a contaminant-free, highly controlled environment by removing air and other gases from a chamber, resulting in a low pressure environment ideal for processes like thin film depositionand ion implantation which enable the creation of the complex structures found in integrated circuits.
Gas & Fluid Equipment:
Advanced semiconductor manufacturers need precision regulation equipment to deliver fluids & gasses for the chip manufacturing process. This equipment is subject to strict manufacturing, purity, and tolerance requirements during fabrication.
Wafer Processing & Automation Components:
As semiconductor and chip manufacturing becomes more precise, so does the handling and automation equipment needed to manipulate, move, and position wafers. Handling equipment and automation components enable seamless transport, alignment, and processing all while reducing potential contaminants and increasing efficiency.
Thermal Control Equipment:
In semiconductor manufacturing environments, there is a critical need for precise temperature and climate control. Thermal management equipment ensures stable conditions to prevent defects.
Purity & Cleanroom Components:
Components for cleanrooms help prevent contamination. Components that are manufactured externally to help maintain a cleanroom in the final production environment require precision and sterile manufacturing conditions.
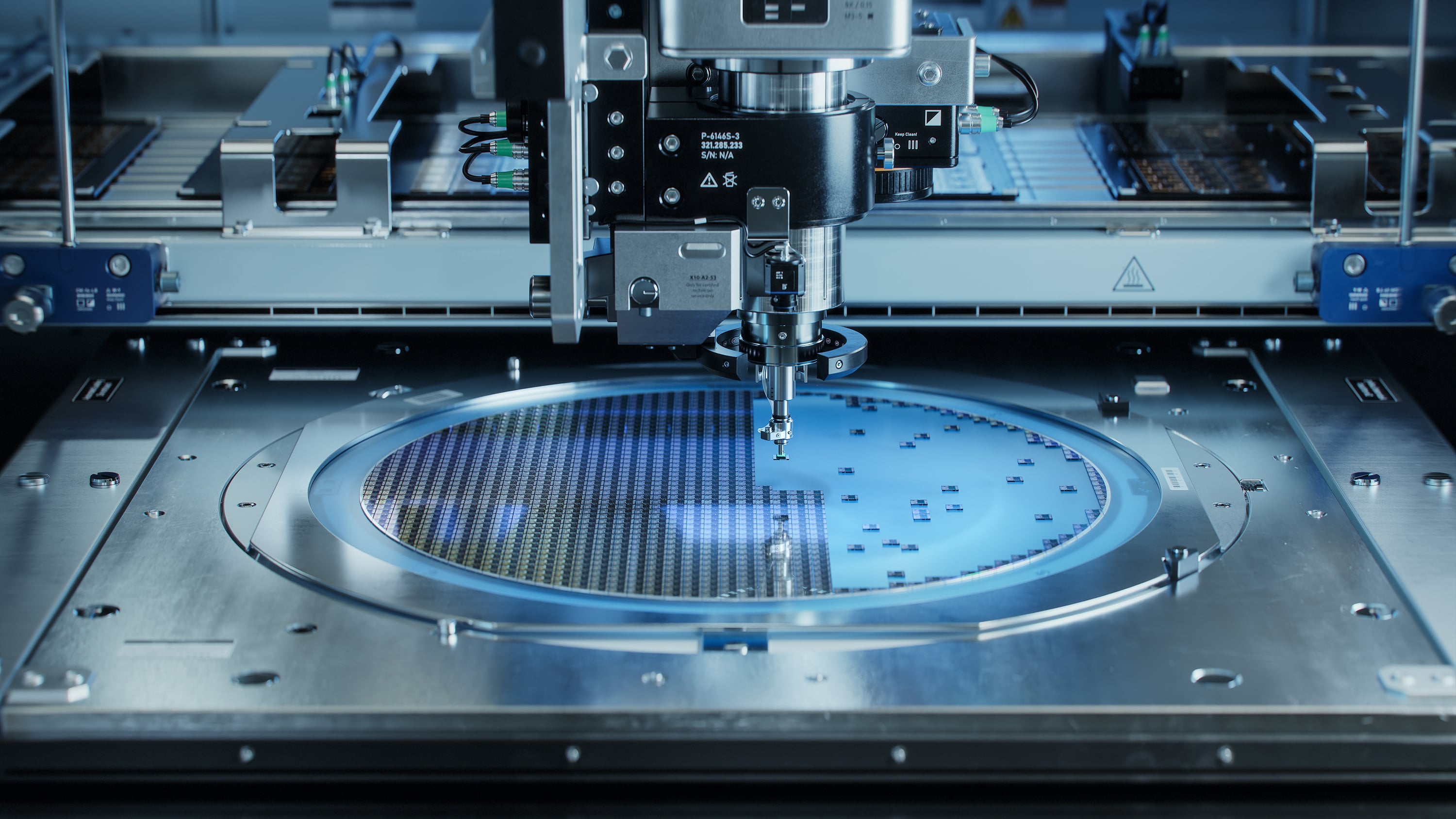
Semiconductor Manufacturing Processes: Casting, Coatings, Oh My!
Precision CNC Machining:
High-tolerance machiningis essential to meet the industry's stringent performance and reliability requirements. Every part plays a crucial role in the final product and must fit perfectly while maintaining extremely tight tolerances
This means the equipment used to make semiconductors must be manufactured using advanced CNC machining, including 5-axis and micro-machining, to produce intricate components with extreme accuracy. These techniques allow for complex geometries and tight tolerances, essential for semiconductor tooling.
Casting:
Semiconductor equipment is often large and complex, and casting processes play a significant role in manufacturing semiconductor equipment like vacuum chamber enclosures, and wafer processing equipment.
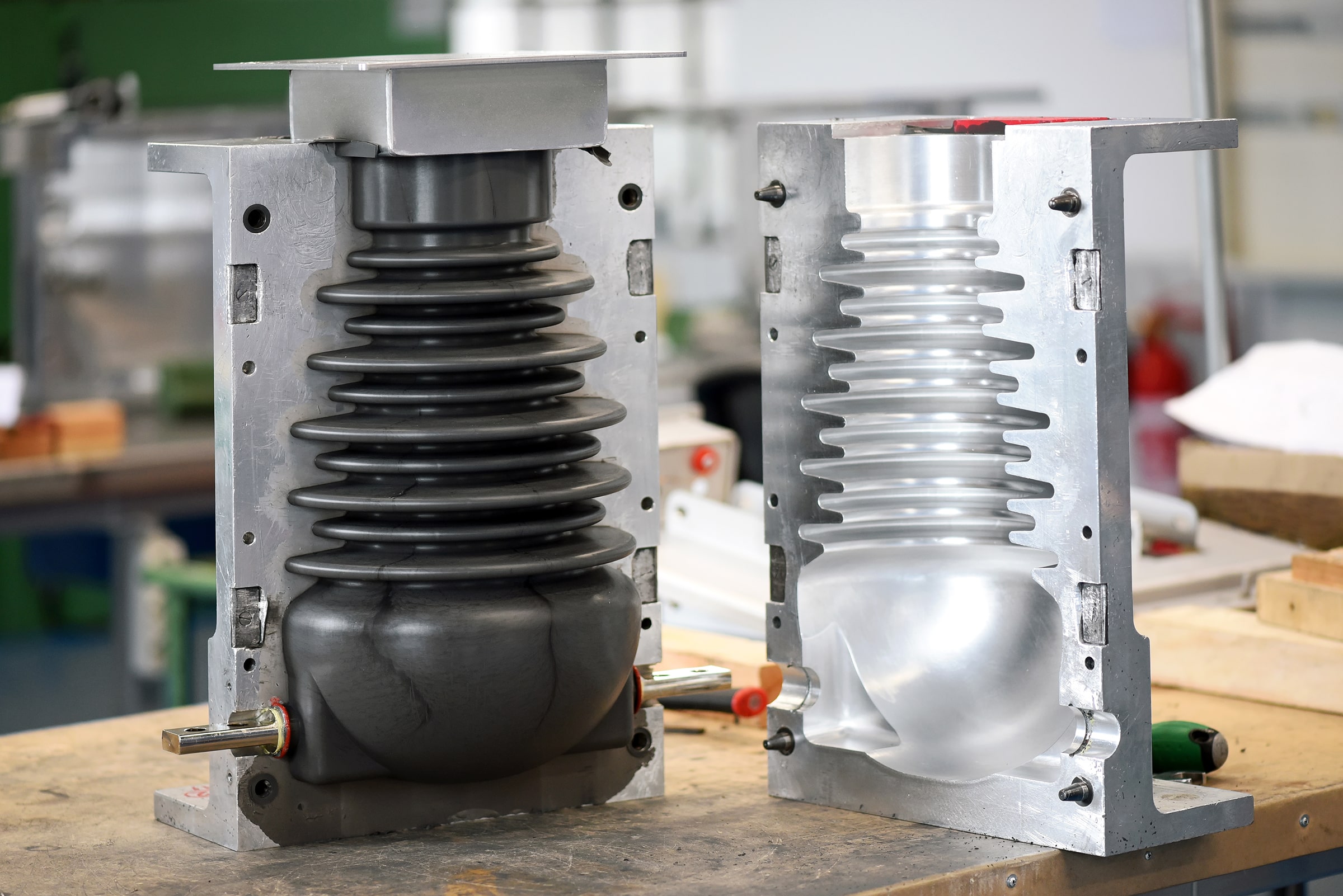
Casting is a process used to create a solid object by pouring a liquefied material, commonly metal, into a mold of the desired shape and then allowed to solidify enabling complex parts to be created in one piece.
Components like stage bases and optical plates (used in wafer processing equipment) require high structural integrity, stability, and specific material properties like purity and corrosion resistance, which casting processes like sand casting, dies casting, and investment casting can provide through a wide range of specialized alloys.
By starting with a near-net shape cast component instead of machining from a solid block, manufacturers can reduce materials waste, the need for extensive machining and offer more cost-effective solutions for complex, high-volume production.
Thermal Spray Coatings:
These coatings protect semiconductor components from heat and wear, ensuring long-term durability.
Other Specialty Processes:
Additional advanced manufacturing techniques, such as plating and anodization, enhance the longevity and performance of semiconductor equipment.
Quality Processes, Testing & Environmental Controls
Helium-Leak Testing:
Ensures airtight seals in vacuum chambers, chip enclosures, and cooling systems by detecting microscopic leaks. This test is often achieved using the vacuum method or sniffer method.
Stress-Testing:
Evaluates semiconductor components under extreme conditions, including thermal cycling, burn-in testing, mechanical stress, and electrostatic discharge testing (ESD).
Sterile Manufacturing Environments & Contamination Control:
Semiconductor manufacturing requires strict quality and environmental control. Temperature, humidity, and microscopic particles can cause defects, so manufacturers use cleanrooms with HEPA and ULPA filtration to maintain air quality. Employees often follow strict gowning protocols to reduce contamination.
ISO 9001 & AS9100 Certifications
Quality is a key concern for the equipment manufacturers, which is why it’s important to look for manufacturing partners who have undergone quality certificationslike ISO 9001 for quality management systems, and AS9100 for aerospace-grade precision manufacturing. Maintaining these quality certifications are third-party assurances that the partners in your supply chain are experts in meeting the compliance and testing requirements needed for semiconductor equipment.
Regulatory Compliance & Industry Standards
Recent geopolitical changes are influencing semiconductor manufacturing strategies worldwide. The U.S. government has implemented policies to encourage domestic semiconductor production, including the CHIPS Act, which allocates over $50 billion for semiconductor research and manufacturing. Additionally, trade tensions and export restrictions have led major semiconductor companies to reevaluate their supply chain strategies.
TSMC, the world's largest semiconductor foundry, has announced plans to invest $100 billion into U.S.-based semiconductor manufacturingto mitigate the impact of tariffs and geopolitical risks. This shift signals a growing trend toward the US onshoring semiconductor supply chains, reducing dependency on foreign suppliers, and enhancing domestic manufacturing capabilities.
Impact of CHIPS Act & Domestic Semiconductor Manufacturing Incentives
For OEMs in the semiconductor industry, this means there are increased opportunities for government grants, tax credits, and training programs. There are currently several open grant programs that are accepting applications for the earmarked funds. These programs bring with them a level of regulatory requirements and compliance that varies between programs, but are focused on several key areas:
Significant U.S. Manufacturing Presence:
Applicants must demonstrate US-based operations or a strategic shift toward onshoring or reshoring.
National Security:
Eligible applicants contribute to US national security by strengthening domestic supply chains, including partnerships with US-based contract manufacturers.
Financial and Technical Capacity:
Applicants must provide detailed financial documents proving project feasibility and alignment with their technical capabilities, which is supported by partnerships with established industry leaders.
Workforce and Skill Development:
Applicants should outline plans to expand expertise in semiconductor manufacturing through workforce development programs that cultivate skilled labor.
Supply Chain Considerations: Risk, Lead Times & Domestic Manufacturing
The supply chain networks involved in creating a semiconductor operation are extremely complex, including dependencies on raw materials, precision components, and equipment for specialized manufacturing processes. In recent history, nearly every sector has seen how easily global disruptions like the COVID-19 pandemic, or geopolitical tensions can affect lead times or even material availability. Semiconductor OEMs are no exception to this.
Identifying areas of your supply chain that can be sourced in North America significantly reduces the risk and lead times associated with offshore suppliers. Of course there are the obvious benefits, like decreasing the effects of international shipping delays, tariffs and trade restrictions. But there are also secondary benefits, like transparency and visibility into your downstream suppliers, allowing you to mitigate disruptions before the impact is significant to your business. North American suppliers often have stronger connections to domestic suppliers even further down-stream, which can help reduce risk from of global events.
Supply Chain Resiliency and Redundancy
Resilience in supply chainsis not a luxury- it’s a necessity. Semiconductor OEMs should focus on creating a diversified supplier base that will allow dynamic shifts to market conditions. Strategic North American partnerships can help add to the resilience of your supply chain by distributing risk.
This can give you access when needed to specialized capabilities like CNC machining, plastic Injection molding, sheet metal fabrication, welding, advanced testing solutions, and integration services.
The semiconductor industry is evolving rapidly, with increasing demand for high-precision components and resilient supply chains. Advanced manufacturing partners play a crucial role in ensuring high-quality, reliable semiconductor equipment production. By leveraging domestic manufacturing expertise and strategic supply chain partnerships, semiconductor OEMs can future-proof their operations against global uncertainties.
Recent Insights
News
Blog
White Papers