Structural Foam Molding
home / capabilities / plastic injection molding / structural foam molding
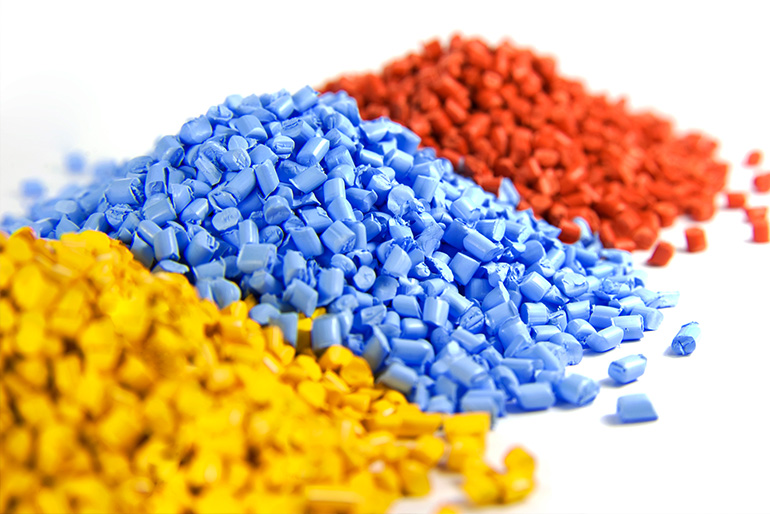
Structurally Sound
Structural foam molding is an injection molding process that creates structurally sound and lightweight parts less likely to warp. Structural foam creates a cellular core and solid outer skin during molding, making it an ideal method for large, thick parts. It is widely used in medical, self-serve kiosk, and industrial markets.
At Cadrex, we have injection molding and sheet metal fabrication experts that can help you convert sheet metal parts to structural foam or form the sheet metal base that supports the structural foam skins in-house.
Benefits of Structural Foam Molding
-
Lighter Weight Parts
-
Decreased Material Costs
-
Increased Part Stiffness and Strength
-
Thick Parts Without Sink Marks
-
Minimal to Zero Warpage
Insight
5 Hints You're Working With The Right Plastic Injection Molding Manufacturer
When it comes to choosing the right plastic injection molding manufacturer, it can be hard to know what you don’t know. Who do you trust? How many questions should you ask? What questions, specifically, should you be asking? With so many variables at play, it’s a challenge to feel like you’re choosing the right manufacturer.
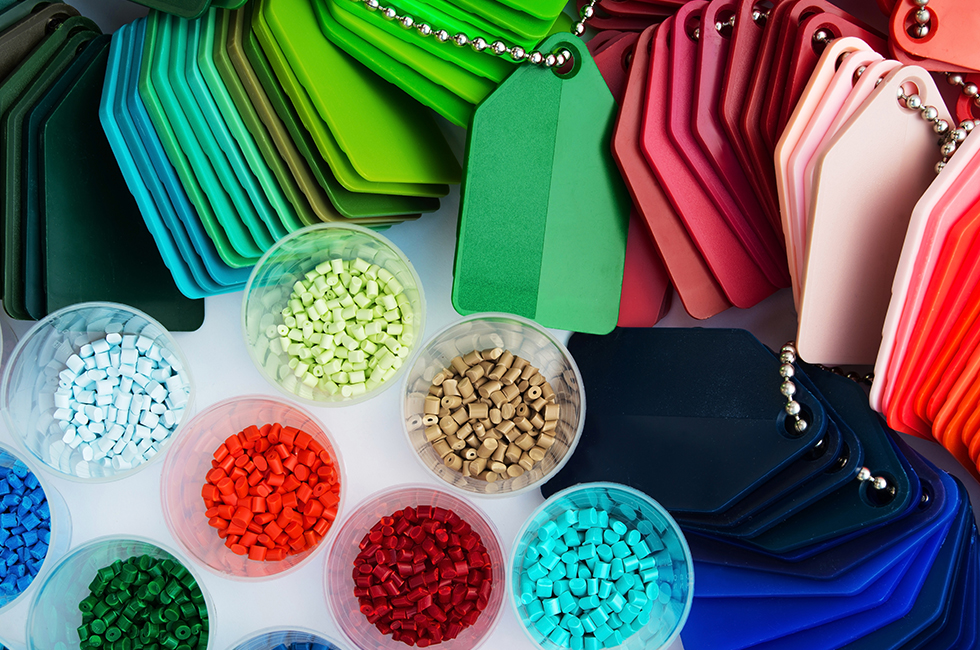
How it Works
Structural foam molding is an injection molding process that creates structurally sound and lightweight parts less likely to warp. A foaming agent is mixed with part resin while still in pellet form. The plastic resin and foaming agent are heated by the barrel in the injection molding machine. Once injected into the mold, the foaming agent turns into gas. The gas bubbles created by the foaming agent expand until the cavity is filled. As the material pushes against the wall of the mold, it creates a thick skin while leaving the inside of the part with a cellular like structure. This not only creates a part that is much lighter than a traditional molded part but also uses less material because of the cellular-like structure.
Due to the unpredictable nature of the gas, structural foam parts have an uneven surface color; you can see tints and shades of the chosen color in a swirl-like pattern. For parts that require high cosmetics, we offer in-house painting services.
Related Links
Blog
Plastic Injection Molding Design Tips
When designing a product, it’s easy to create something that fits all requirements for the product's intent without any thought about the manufacturing process. Many times, it might not be clear what manufacturing process...
White Paper
A Starter Guide To Injection Molding
It is easy to brush over the basics of plastic injection molding and start talking about the benefits, especially when...
Blog
Why Regional Supply Chains Make Sense For Injection Molded Products
Looking for plastic injection molding companies but don't know where to start? Here's why the highest quality, most cost-effective molded parts are usually sourced in North America...